Aluminum Fluxes 101 - Basics of Furnace Cleaning, Dross Handling and Wall Cleaning
Casting defects, energy usage, metal recovery, ergonomics, and labor are cost variables addressed by properly identifying and applying fluxes for the aluminum casting operation. Proper selection and application are especially important to realize the benefits that flux can provide.
Defects stemming from the use of dirty metal are plentiful. Metallic aluminum is very reactive with atmospheric oxygen, and a thin passivation layer of aluminum oxide (4 nm thickness) forms on any exposed aluminum surface in a matter of hundreds of picoseconds to form aluminum oxide (Al2O3). Hydrogen forms whenever molten aluminum meets water vapor, and easily dissolves into the melt. The gas tends to come out of the solution and forms bubbles when the melt solidifies. The detrimental effects arising from the presence of an excess of dissolved hydrogen in aluminum are numerous. Aluminum oxide and hydrogen gas H2 are the two most common defects found in aluminum castings. Magnesium formation is also common in aluminum melting due to reaction with the alloy or with the refractory which typically contains magnesium and oxidizes rapidly forming magnesium aluminate (spinel), which visually forms black speck inclusions in the metal surface. Aluminum fluxes will address all three potential inclusions from the process of melting to final molten metal preparation. This article will cover two of the seven fluxes listed below*, drossing and wall cleaning fluxes, and some of the key savings.
Optimizing Your Foundry Operation Via Optimized Risering Practice
By the end of 2020 many hoped that 2021 would be a rebounding year for the metal casting industry. On the contrary the stark reality is that 2021 has proven to be one of the toughest years that the metal casting industry has ever experienced.
The reality of rapid cost escalation for raw materials was quickly worsened by news of shortages and tight supply of key raw materials to make finished goods. If the cost escalations were not enough, when raw materials could be found and purchased (even at very high prices), ensuring a reliable supply chain was nearly impossible. Products that routinely carried a lead time of four weeks were suddenly being delayed 10 to 12 weeks, with no prior notice. The situation is particularly tight for materials being sea-freighted, which has triggered significant back logs in trucking and rail. There are many motives associated with this surge in prices and tight supply, from the disruptions in sea-freight in the Suez Channel, big backlogs in entry ports, deep freezes in the gulf region, to traversing many geopolitical situations. The situation has turned even more critical as the pent up demand for products and services has risen steadily throughout the year.
Next-Generation Chromite Sand
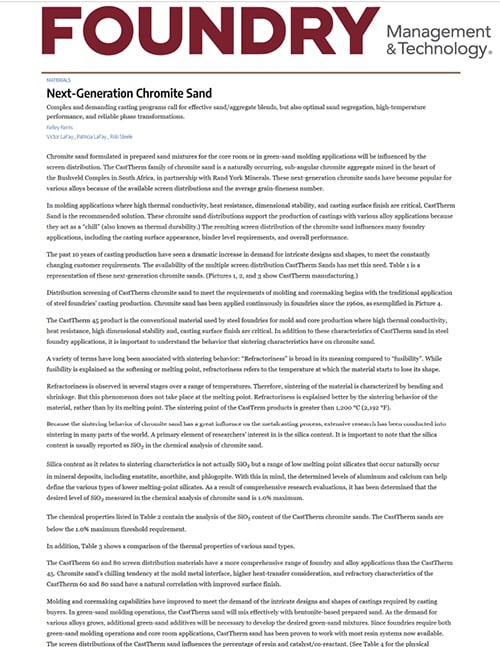
Chromite sand formulated in prepared sand mixtures for the core room or in green-sand molding applications will be influenced by the screen distribution. The CastTherm family of chromite sand is a naturally occurring, sub-angular chromite aggregate mined in the heart of the Bushveld Complex in South Africa, in partnership with Rand York Minerals. These next-generation chromite sands have become popular for various alloys because of the available screen distributions and the average grain-fineness number.
In molding applications where high thermal conductivity, heat resistance, dimensional stability, and casting surface finish are critical, CastTherm Sand is the recommended solution. These chromite sand distributions support the production of castings with various alloy applications because they act as a "chill" (also known as thermal durability.) The resulting screen distribution of the chromite sand influences many foundry applications, including the casting surface appearance, binder level requirements, and overall performance.
Optimizing Your Foundry Operation Via Optimized Risering Practice
Exothermic and insulating feeding systems (or feeders) are common practice in our industry. With the development of modern high production molding equipment, we have accepted the challenges in developing feeding aids for these new systems.
Innovative rigging systems have also helped foundries improve productivity by increasing the number of castings per mold. Although this is a positive economic change, it limits positioning, sizing and feeder contact area on the pattern plate, making it challenging for the foundry engineer to produce shrink-free castings. Advancements in manufactured feeding aids are trying to meet the challenges foundries face by balancing improved processes, productivity demands and costs while maintaining high quality castings.
Cutting Edge Feeding Technology for Advanced Casting Processes
The use of exothermic and insulative feeding systems - sleeves and pouring cups - have been common practice for many years. Increasingly over the last three decades, foundries have improved productivity by increasing the number of castings per mold. This economical change has resulted in more restrictive positioning of the feeding sytems on the pattern plate.
This reduction in feeder size and contact area makes it challenging to maintain feeding performance. Advancements in manufactured feeding solutions continue to be developed to meet these challenges foundries face with balancing improved processes, productivity and costs while maintaining high quality castings.
Phenolic Urethane Cold Box Environmental Advantages
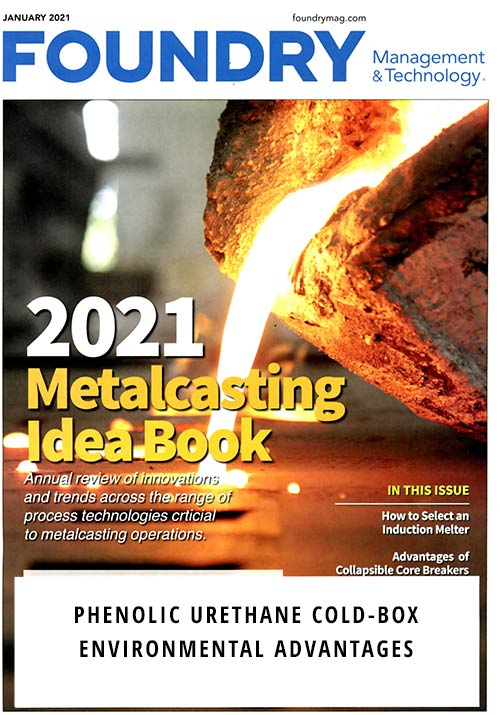
The Phenolic Urethane Cold Box process (PUCB) is the most widely used, organic chemical process for coremaking in North America. Its reputation for being versatile, highly productive, and cost efficient are the reasons it remains popular today, especially for metalcasting in the automotive, mining, and agricultural supply chains.
The appreciation for PUCB systems primarily comes from these benefits: faster cycle times; applicability for ferrous and nonferrous casting; excellent performance for highly complex cores; high mechanical strength; and effective thermal characteristics.
5 Keys to Reducing Casting Defects Through Refractory Coatings
Phenolic Urethane Cold Box Process
Reducing Shrinkage in Aluminum Castings With Resin Selection
As casting geometries become thinner in design and more complex, the influences from resin selection will place a more crucial role in providing a solid casting. An aluminum foundry was experiencing issues with a dendritic type shrinkage defect that was related to a recent change in a resin package, resulting in higher scrap rates from the shrink defect.
The only variable that changed and created the dendritic type shrink defect in this case was the resin. HA-International designed an experiment to determine how PUCB resin percentages, and solvent packages used in urethane cold boxes affected the influence of shrink on this particular aluminum A316 casting during solidification.
Evaluation occurred on a newly developmental phenolic urethane cold box and a modified version of this new system, utilizing the latest solvent packages found in HAI's SigmaCure series of phenolic urethane cold box (PUCB). The experimental setup of the study included computer aided modeling, analytical testing, and actual casting tests to generate cooling curves. These results, in conjunction with the temperature dependent properties were used to create simulation model datasets for the cold box sand mix in order to simulate the actual sand mold physical properties and understand how it was creating the shrinkage defects. Between 1,500-2,000 design iterations were conducted in modeling software to obtain a dataset that matched the results from actual lab casting results. The specific heat capacity and density results required for the simulation datasets were measured directly using instrumentation on test molds.
Optimized Feeding Systems

It is well known that metals change volume during solidification. This volume change must be compensated during solidification otherwise shrinkage defects can occur in a casting, making it unusable for its stated purpose.
This has been solved through the use of adding a metal reservoir commonly known as a "feeder" the purpose of which is to supply liquid metal to the casting as it cools and solidifies.
As this technology has developed and been improved, newer types of feeder materials have become available, including combinations of exothermic-insulating and highly exothermic compositions. The choice of material depends upon the application.
Environmental stewardship: NOT JUST A TREND
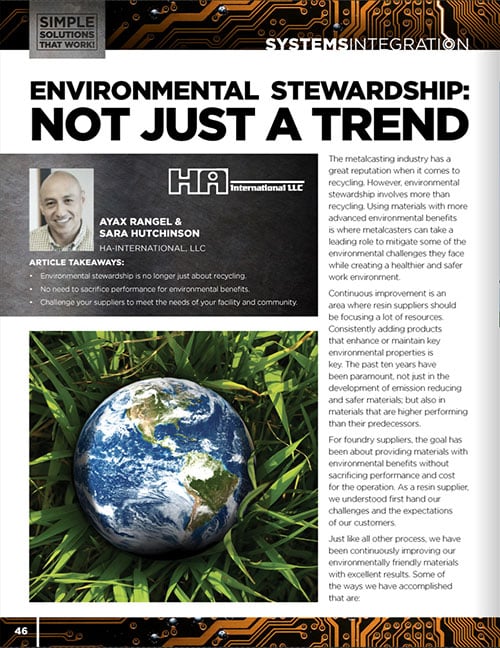
Evolution of Foundry Shell Sand for Today's Foundry
Simple Solutions That Work - (Issue 9, September 2018)
The Shell Sand process or "Croning" process was invented by Dr. Johannes Croning in Hamburg, Germany in 1944. This process is the oldest core and mold making technology that utilizes synthetic resins. Although many additional sand core and molding making technologies have since been introduced, the Shell Sand process is still a very effective core and molding process today.
An Interesting Approach to the Product Installation Process
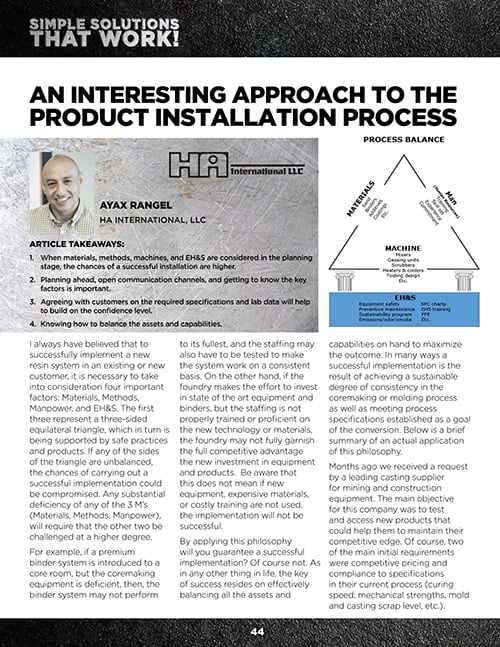