Cutting Edge Feeding Technology for Advanced Casting Processes
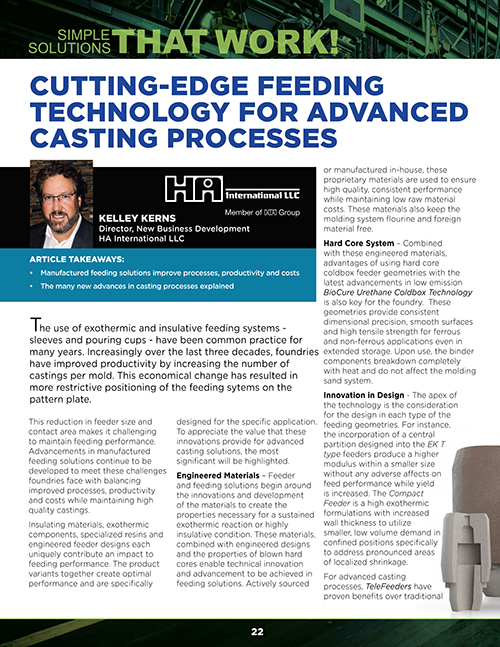
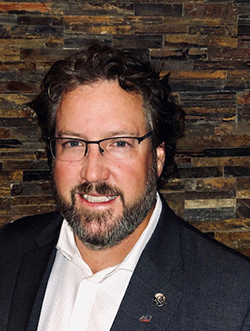
KELLEY KERNS | Spring 2021
Reprinted with permission from Simple Solutions That Work!
Download PDF: English
- Manufactured feeding solutions improve processes, productivity and costs
- The many new advances in casting processes explained
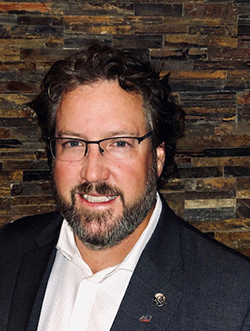
The use of exothermic and insulative feeding systems - sleeves and pouring cups - have been common practice for many years. Increasingly over the last three decades, foundries have improved productivity by increasing the number of castings per mold. This economical change has resulted in more restrictive positioning of the feeding sytems on the pattern plate.
This reduction in feeder size and contact area makes it challenging to maintain feeding performance. Advancements in manufactured feeding solutions continue to be developed to meet these challenges foundries face with balancing improved processes, productivity and costs while maintaining high quality castings.
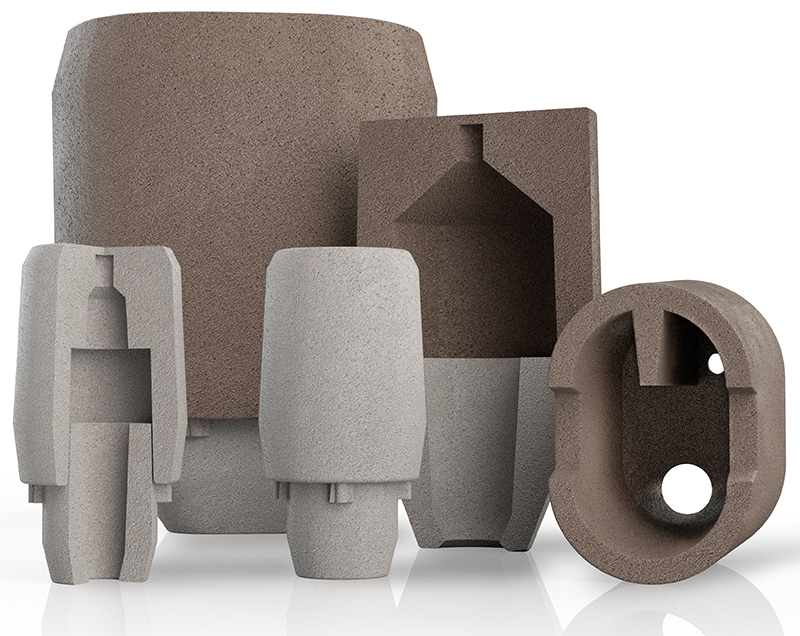
Insulating materials, exothermic components, specialized resins and engineered feeder designs each uniquely contribute an impact to feeding performance. The product variants together create optimal performance and are specifically designed for the specific application. To appreciate the value that these innovations provide for advanced casting solutions, the most significant will be highlighted.
Engineered Materials - Feeder and feeding solutions begin around the innovations and development of the materials to create the properties necessary for a sustained exothermic reaction or highly insulative condition. These materials, combined with engineered designs and the properties of blown hard cores enable technical innovation and advancement to be achieved in feeding solutions. Actively sourced or manufactured in-house, these proprietary materials are used to ensure high quality, consistent performance while maintaining low raw material costs. These materials also keep the molding system flourine and foreign material free.
Hard Core System - Combined with these engineered materials, advantages of using hard core coldbox feeder geometries with the latest advancements in low emission BioCure Urethane Coldbox Technology is also key for the foundry. These geometries provide consistent dimensional precision, smooth surfaces and high tensile strength for ferrous and non-ferrous applications even in extended storage. Upon use, the binder components breakdown completely with heat and do not affect the molding sand system.
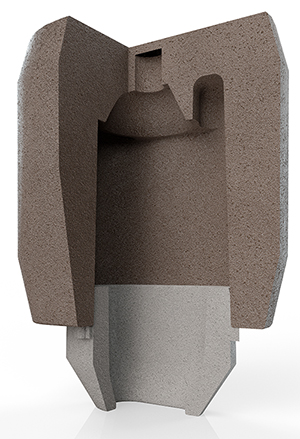
Innovation in Design The apex of the technology is the consideration for the design in each type of the feeding geometries. For instance, the incorporation of a central partition designed into the EK T type feeders produce a higher modulus within a smaller size without any adverse affects on feed performance while yield is increased. The Compact Feeder is a high exothermic formulations with increased wall thickness to utilize smaller, low volume demand in confined positions specifically to address pronounced areas of localized shrinkage.
For advanced casting processes, TeleFeeders have proven benefits over traditional feeding systems. The principle of this unique design, used in horizontally parted molding applications, allows the upper section to telescopically slide over the lower section during the compaction process minimizing pressure to the lower section and avoiding any breakage. This compressing of the upper section leads to additional compaction of the molding sand in the transition areas between the feeder and the casting, precisely where poorly compacted sand may occur in other feeding systems. The two piece system also can be used to further optimize the feeder's performance. The upper part of the feeder is shaped to increase modulus and as a factor of geometrical calculation, holds less liquid versus traditional feeders. The lower part keeps the metal contained within the feeder liquid and extends the feeder solidification time to a greater degree than feeders without a feeder neck using exothermic materials. The oval and round contacts used in telefeeders are designed to allow access to hidden surfaces close to hot spots. These designs allow placement of the feeder where efficiency is the highest and is a critical path to meeting quality requirements of today's castings. Flexibility to use different exothermic formulas which are specific to the casting application, add critical exothermic heat in the neck area--the heart of the feeding—and distinguish TeleFeeders from other feeders and risers available on the market.
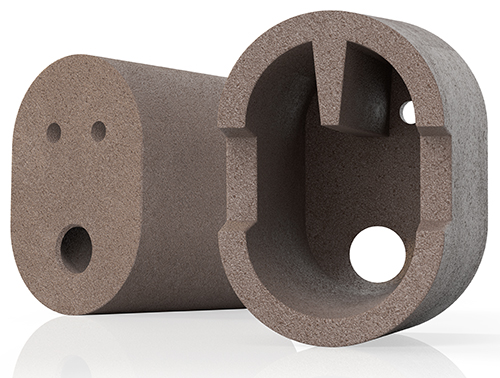
Aluminum Application - The same TeleFeeder are now being utilized for aluminum and other non-ferrous casting in automatic green sand molding applications. By applying the TeleFeeder designs and changing the formula to insulating, beneficial results are available for the aluminum casting. The lower section can be modified to meet the feeding requirements while also contributing to the ease of riser removal. As with the ferrous application, the TeleFeeder is designed to collapse and not crush under the pressure of automatic molding. TeleFeeder technology for aluminum applications offer molten metal feeding for elimination of chills in providing sound castings.
Side Insert Feeder - This new side insert feeder is an engineered solution to enable feeding of cross sections where the hot spot area has not been accessible with a sand riser installed on the pattern. The new one-piece side insert feeder is not molded onto the pattern plate, instead it is inserted into the mold by the core setter. It allows placement on any area of the casting and makes testing and modification achievable. The cycle time on automatic machines stays the same—with no slow down—and adds a highly valuable component in the solidification process.
The feeder works for all castings where the side feeder can be positioned on the mold partition. At the same time, it frees up additional space on the pattern plate for more impressions on the existing real estate which provides lead time and productivity improvements.
Given the exothermic properties, the efficiency of this technology is much higher than sand feeders. Because less feeding mass is required, it is now possible to produce more castings with the same production capacity while improving yields.
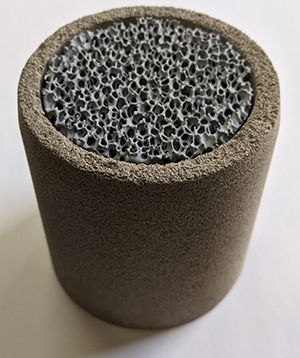
Another advantage is that the geometry of the feeder provides directional solidification. The contact area between the feeder and the casting is optimized and contact area is reduced at the same time. This makes it easier to break off the riser and significantly reduces cleaning costs. In addition, two small openings provide excellent ventilation during pouring reducing the potential of gas defects.
Filtrated Pouring Cups or FPCs - Introduced recently to the market, this innovation offer advantages over fiber or shell pouring sprues and basins. The FPCs are blown in coldbox and provide exact and repeatable dimensions with a patented insulating material manufactured in-house providing improved properties over existing insulative materials. Ensuring a clean pouring basin with an incorporated designated PPI filter saves time while safeguarding metal contamination. Additionally, the FPC can extend the pouring basin beyond the green sand or no-bake mold in applications where extra pattern height is needed for head pressure or increased flexibility in pattern layout is advantageous.
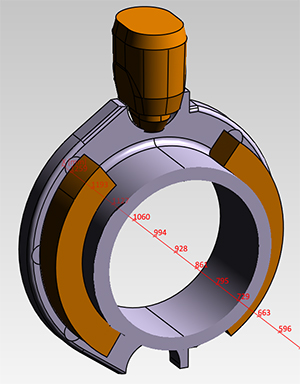
Reverse Taper Direct Pours - Another innovative product recently introduced to the market is the Reverse Taper Direct Pours. This combination of both feeding and filtration utilizes one product that offers opportunities to maximize pattern real estate while promoting clean metal, improved foundry yield and casting quality. The Direct Pour unit consists of a combination insulating sleeve with an incorporated filter as part of the advanced design. The reverse taper design is ideal for automated green sand molding applications.
Customized Contour Cores - Fully customizable, contour cores provide extended feeding area via core shapes that form the casting surface using an exothermic material, effectively creating a larger gradient of feeding modulus under a feeder. These also deliver an easy to use option for areas that are limited in space for feeding due to height or casting shape. By changing the formula, it performs as a chill core providing a moderate amount of chilling that matches exactly to a casting surface.
In the overall casting production process and drive for advanced manufacturing processes, feeding systems are instrumental in producing a lower cost, sound casting whether for vertical and horizontal green sand, no-bake or semi-permanent molding processes. Considering the novelty in design and engineered materials, each innovation offers increased flexibility and uniqueness in approach that matches with the needs of today’s engineering and advancing casting processes.