Next-Generation Chromite Sand
Chromite sand formulated in prepared sand mixtures for the core room or in green-sand molding applications will be influenced by the screen distribution. The CastTherm family of chromite sand is a naturally occurring, sub-angular chromite aggregate mined in the heart of the Bushveld Complex in South Africa, in partnership with Rand York Minerals. These next-generation chromite sands have become popular for various alloys because of the available screen distributions and the average grain-fineness number.
In molding applications where high thermal conductivity, heat resistance, dimensional stability, and casting surface finish are critical, CastTherm Sand is the recommended solution. These chromite sand distributions support the production of castings with various alloy applications because they act as a "chill" (also known as thermal durability.) The resulting screen distribution of the chromite sand influences many foundry applications, including the casting surface appearance, binder level requirements, and overall performance.
The past 10 years of casting production have seen a dramatic increase in demand for intricate designs and shapes, to meet the constantly changing customer requirements. The availability of the multiple screen distribution CastTherm Sands has met this need. Table 1 is a representation of these next-generation chromite sands. (Pictures 1, 2, and 3 show CastTherm manufacturing.)
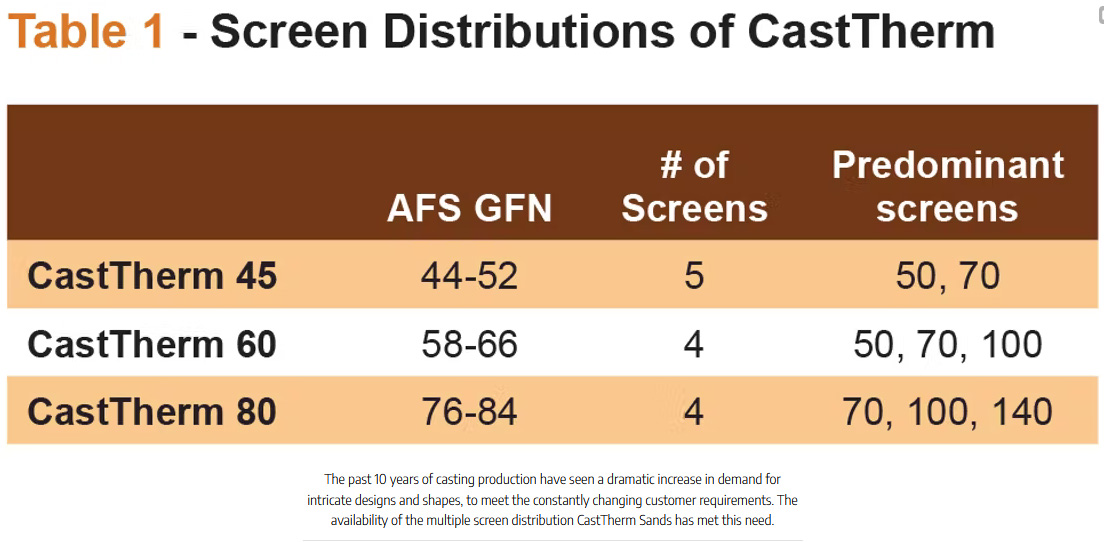
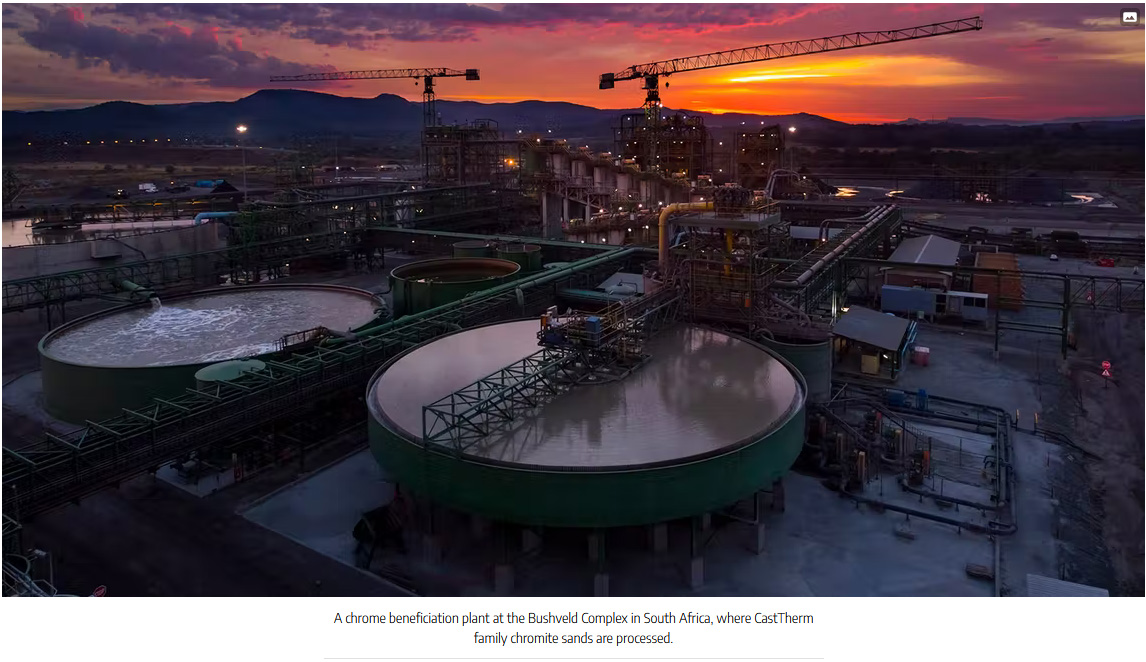
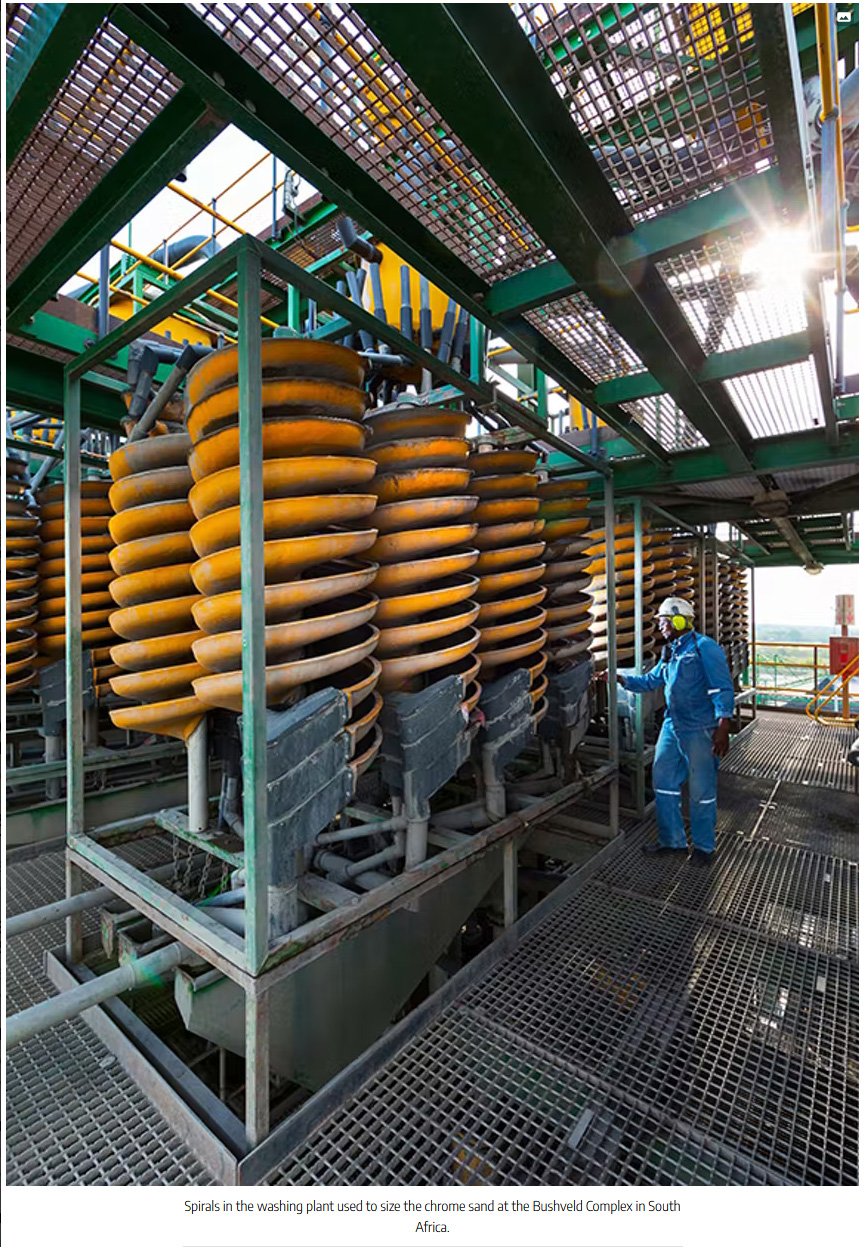
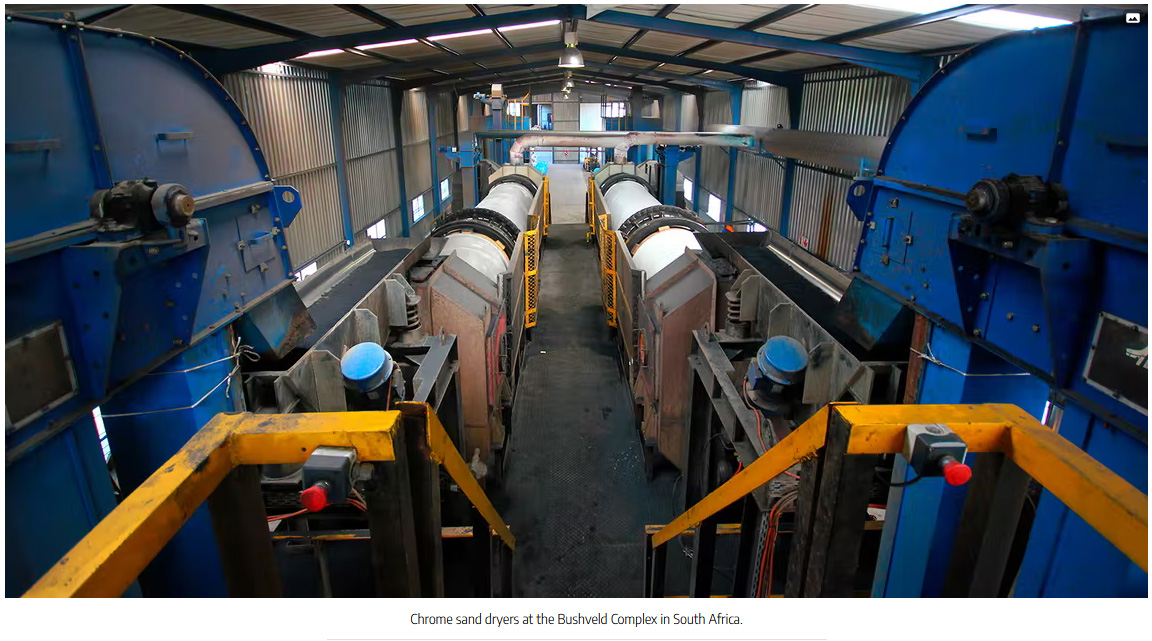
Distribution screening of CastTherm chromite sand to meet the requirements of molding and coremaking begins with the traditional application of steel foundries’ casting production. Chromite sand has been applied continuously in foundries since the 1960s, as exemplified in Picture 4.
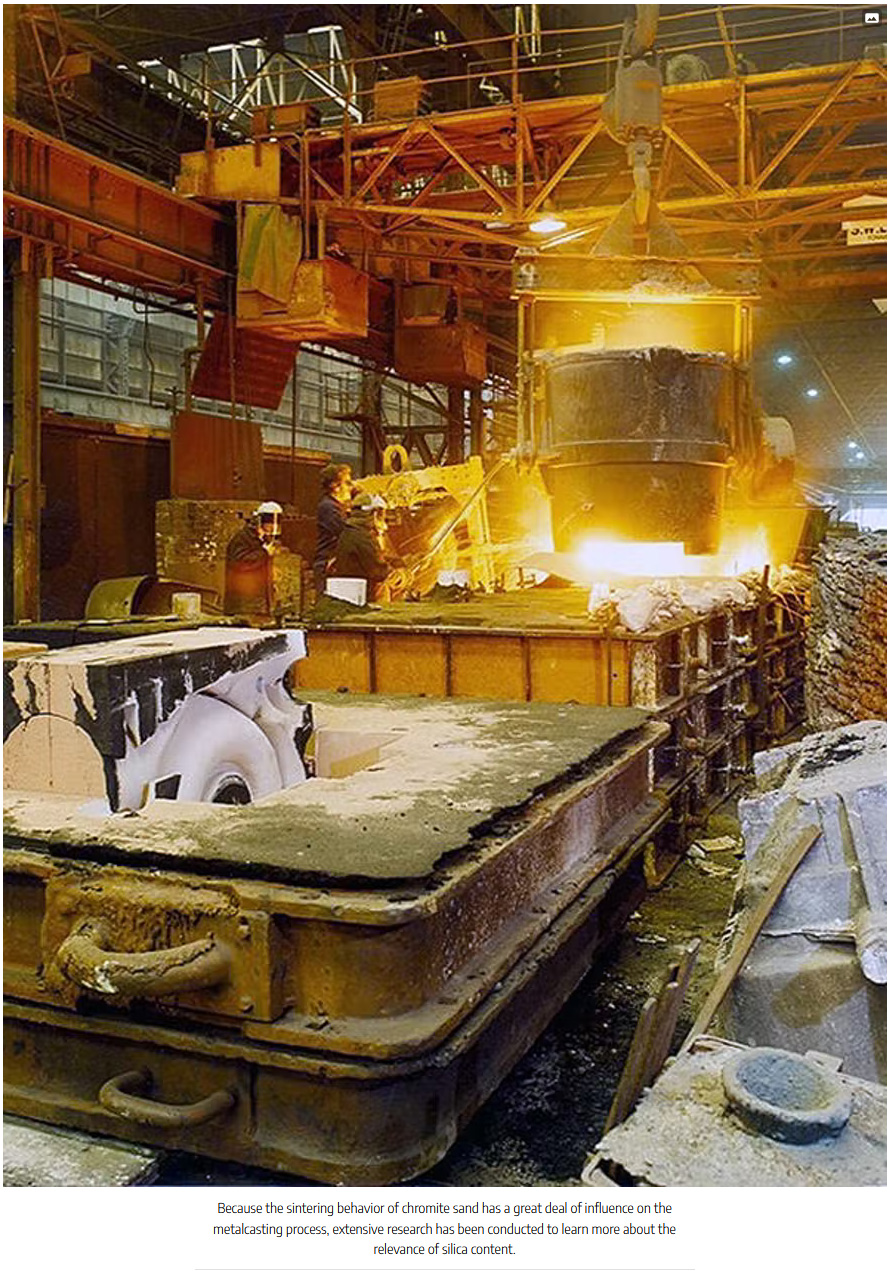
The CastTherm 45 product is the conventional material used by steel foundries for mold and core production where high thermal conductivity, heat resistance, high dimensional stability and, casting surface finish are critical. In addition to these characteristics of CastTherm sand in steel foundry applications, it is important to understand the behavior that sintering characteristics have on chromite sand.
A variety of terms have long been associated with sintering behavior: "Refractoriness" is broad in its meaning compared to "fusibility". While fusibility is explained as the softening or melting point, refractoriness refers to the temperature at which the material starts to lose its shape.
Refractoriness is observed in several stages over a range of temperatures. Therefore, sintering of the material is characterized by bending and shrinkage. But this phenomenon does not take place at the melting point. Refractoriness is explained better by the sintering behavior of the material, rather than by its melting point. The sintering point of the CastTerm products is greater than 1,200 °C (2,192 °F).
Because the sintering behavior of chromite sand has a great influence on the metalcasting process, extensive research has been conducted into sintering in many parts of the world. A primary element of researchers’ interest in is the silica content. It is important to note that the silica content is usually reported as SiO2 in the chemical analysis of chromite sand.
Silica content as it relates to sintering characteristics is not actually SiO2 but a range of low melting point silicates that occur naturally occur in mineral deposits, including enstatite, anorthite, and phlogopite. With this in mind, the determined levels of aluminum and calcium can help define the various types of lower melting-point silicates. As a result of comprehensive research evaluations, it has been determined that the desired level of SiO2 measured in the chemical analysis of chromite sand is 1.0% maximum.
The chemical properties listed in Table 2 contain the analysis of the SiO2 content of the CastTherm chromite sands. The CastTherm sands are below the 1.0% maximum threshold requirement.
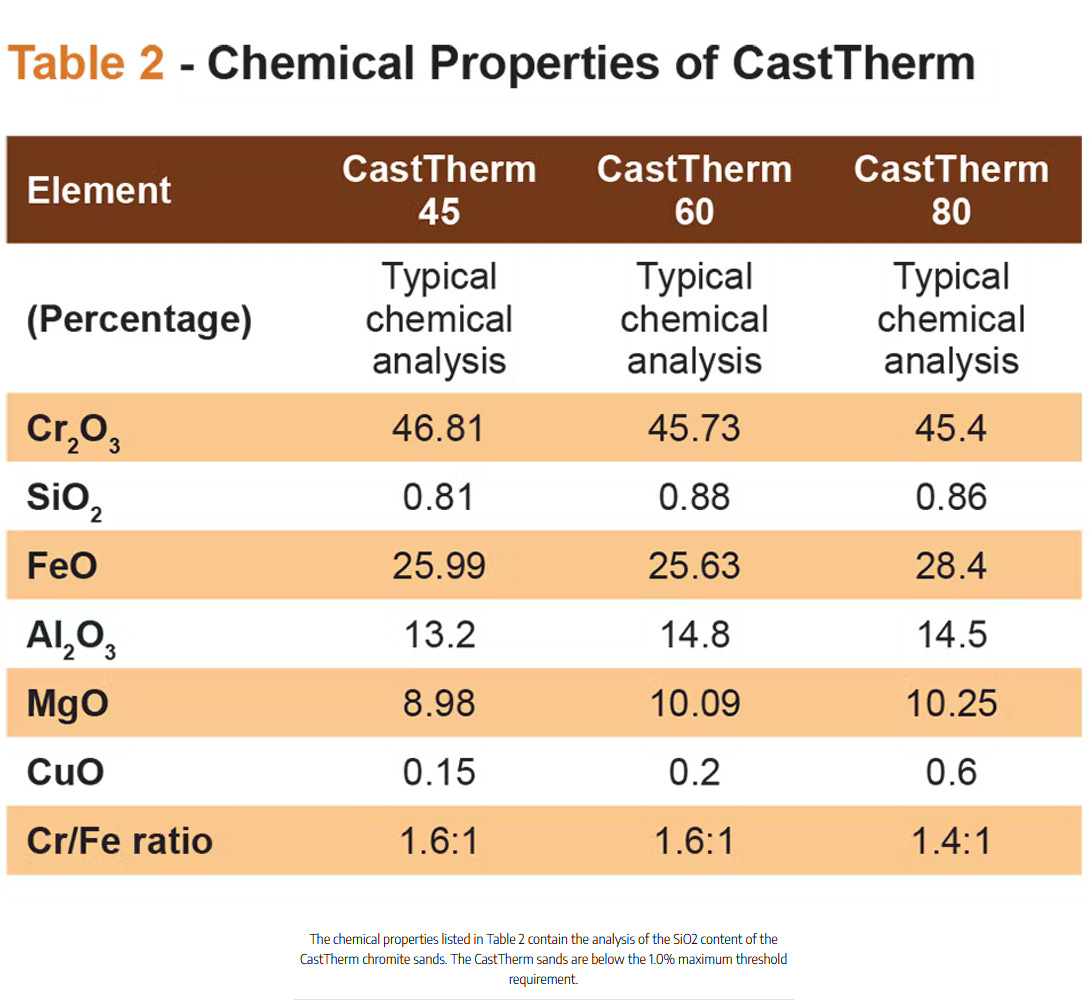
In addition, Table 3 shows a comparison of the thermal properties of various sand types.
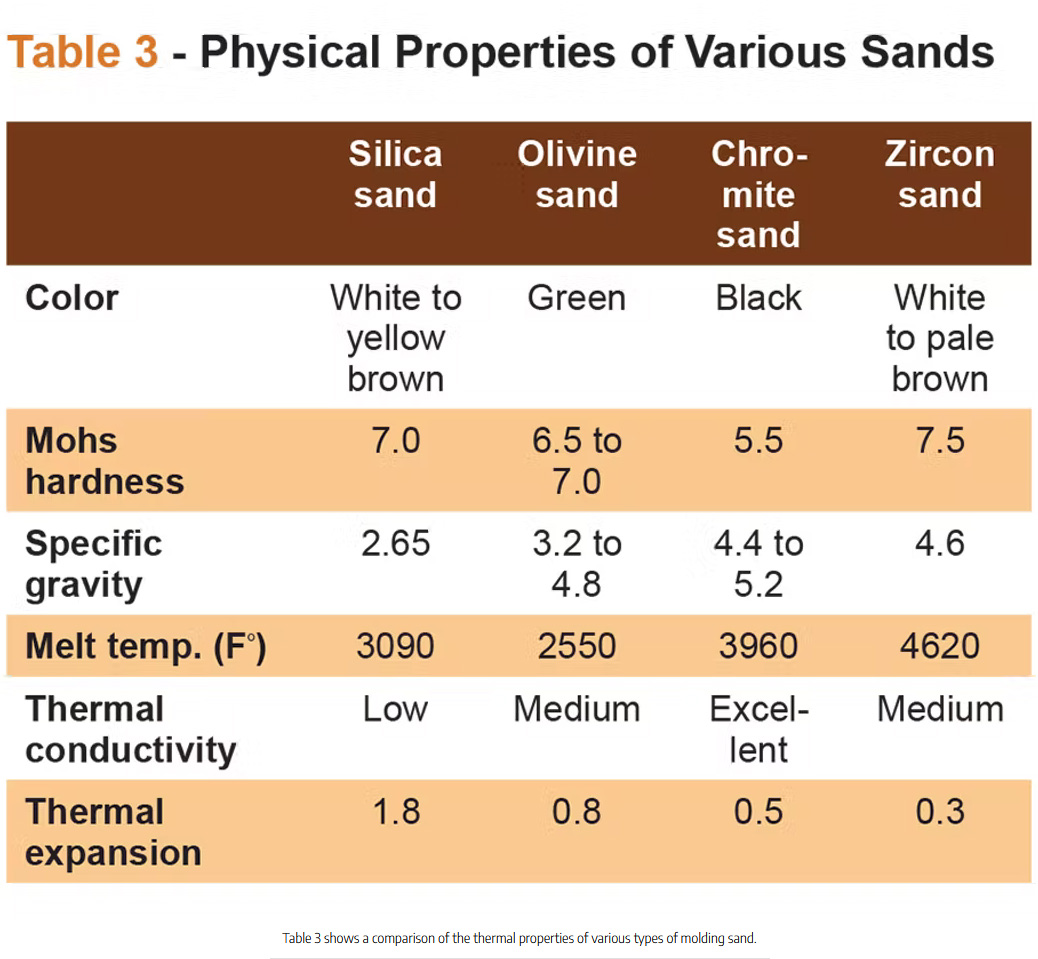
The CastTherm 60 and 80 screen distribution materials have a more comprehensive range of foundry and alloy applications than the CastTherm 45. Chromite sand’s chilling tendency at the mold metal interface, higher heat-transfer consideration, and refractory characteristics of the CastTherm 60 and 80 sand have a natural correlation with improved surface finish.
Molding and coremaking capabilities have improved to meet the demand of the intricate designs and shapes of castings required by casting buyers. In green-sand molding operations, the CastTherm sand will mix effectively with bentonite-based prepared sand. As the demand for various alloys grows, additional green-sand additives will be necessary to develop the desired green-sand mixtures. Since foundries require both green-sand molding operations and core room applications, CastTherm sand has been proven to work with most resin systems now available. The screen distributions of the CastTherm sand influences the percentage of resin and catalyst/co-reactant. (See Table 4 for the physical properties of CastTherm sands.)
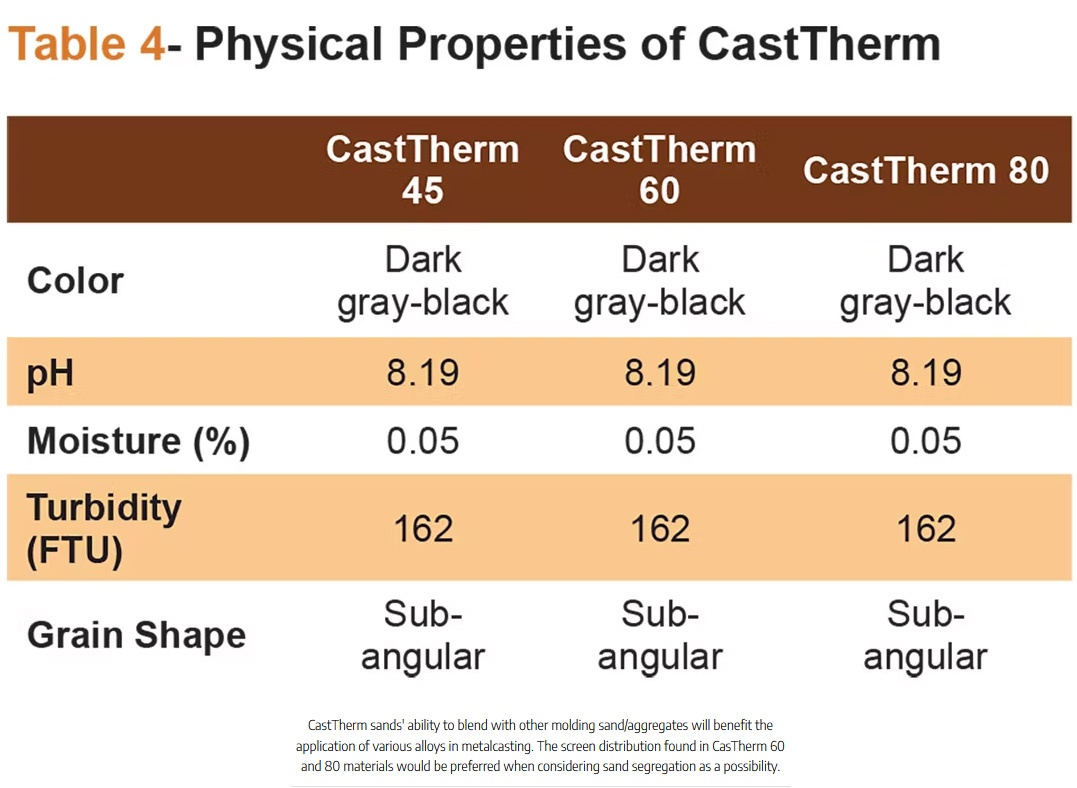
The ability to blend the CastTherm sands with other molding sand/aggregates will benefit applications of various alloys by foundries. The screen distribution found in CasTherm 60 and 80 materials would be preferred when considering sand segregation as a possibility, as frequently suggested in research published and presented over the past decade. More specifically, numerous conference publications have suggested that:
- The quality of metalcastings is related to the high-temperature performance of the refractory aggregates used.
- Molding aggregates that do not exhibit rapid changes in volume due to phase transformations provide for more predictable final casting dimensions. Reducing these rapid changes lowers the surface strain on the mold surface and reduces the associated defects.
- The use of sand blends of inexpensive silica sand with higher-cost specialty sands has proven to have applications where the quality of the casting can be improved without the associated high cost of 100% specialty sand cores.
CastTherm chromite sand offers a full range of sand distributions that are specifically mined and processed to meet foundry’s future needs, and to support casting design requirements.
Kelley Kerns is the director of new business development at HA International LLC. Contact him at sales@ha-international.com, or visit www.ha-international.com
Rob Steel is the president of F.A.C.T. LLC. Vic and Pat Lafay are partners in Common Sense Applications LLC.